Manufacturing has an unprecedented opportunity to optimize its operations and stay one step ahead of ever-evolving customer demands. By leveraging the latest tools in 3D configuration, manufacturers have a powerful way to increase efficiency, reduce costs, and improve accuracy across their business.
With the addition of digital configurators into manufacturing processes, companies from all industries can benefit from faster order times, and reduced design time for custom products and services tasks – yielding maximum return on investment while keeping customers satisfied with accuracy that was previously difficult or impossible to achieve.
In this blog post, we will explore the possibilities that 3D configuration offers for streamlining your manufacturing operations: what it is; how it works; and why you might choose this technology over others in your production processes.
What is a 3D Configurator and what are the benefits of using one in manufacturing processes
As technology advances, manufacturing companies are constantly seeking ways to streamline their processes and increase efficiency. One innovative tool that has emerged in recent years is the 3D Configurator.
A 3D Configurator is a software program that allows users to create customized products by selecting different options from a pre-set menu. This tool has numerous benefits for manufacturers, including increased accuracy, reduced production time, and lowered costs.
By eliminating the need for physical prototypes and allowing for quick and easy design changes, the 3D Configurator can revolutionize how companies approach their manufacturing processes. As competition in the industry increases, those who integrate this technology into their operations are more likely to stay ahead of the curve.
How it supports cost-effective and streamlined production
Utilizing 3D configurators streamlines the entire manufacturing process by optimizing various aspects:
- Reduced Design Time: With 3D configurators, product design takes less time as designers can quickly create and modify models without manual adjustments. This expedites the design phase and accelerates the development process.
- Improved Quality Control: By visualizing how components fit together in the 3D model, designers can identify potential issues early, reducing errors during manufacturing and ensuring product quality.
- Faster Prototyping: Automated assembly within the software eliminates the need for physical prototypes, allowing for rapid prototyping and faster iteration cycles.
- Enhanced Collaboration: Cloud-based systems enable real-time data sharing among different teams, facilitating seamless collaboration, and ensuring everyone is on the same page throughout the manufacturing process.
- Increased Flexibility: The ability to make quick changes within the 3D model promotes experimentation with different designs, enabling manufacturers to adapt to market demands efficiently
- Automated Bill of Materials: 3D configurators generate automated bills of materials, simplifying the tracking of component costs and streamlining inventory management.
- Reduced Material Waste: Less reliance on physical prototypes results in lower material waste and cost savings during the manufacturing process.
- Faster Time to Market: Automation of processes like prototyping and testing shortens product development cycles, allowing manufacturers to bring new products to market quicker.
- Improved Cost Estimation Accuracy: Real-time access to component cost data ensures more accurate cost estimates, enabling better budget management and cost optimization.
- Enhanced Visualization Capabilities: 3D visualizers and configurators provide detailed visualization from multiple angles, aiding in identifying part interactions and potential improvements in the manufacturing process.
By incorporating 3D configurators into manufacturing operations, companies can achieve greater efficiency, reduced production times, and improved product quality, ultimately streamlining the entire manufacturing workflow.
The advantages of accuracy and quick delivery when using a 3D Configurator
How to select the best 3D Configurator for your manufacturing needs
Understand Your Product Requirements
The first step in selecting the best 3D configurator for your manufacturing needs is to understand your product requirements. This includes the type of product you are manufacturing, the size and shape of the product, and any other features that need to be taken into consideration. Additionally, you should consider any special requirements such as customizations or specific materials that must be used.
Research Available Configurators
Once you have a good understanding of your product requirements, it is time to research available configurators. Look for configurators that offer features and capabilities that match your needs, such as CAD integration, advanced customization options, and support for different file formats. Additionally, consider factors such as cost and ease of use when comparing different configurators.
Test Out Different Configurators
Consider Technical Support Options
Think About Scalability
It is also important to think about scalability when selecting a 3D configurator for your manufacturing needs. If you plan on expanding production in the future, make sure that the software you choose can scale up with increased demand without requiring major changes or upgrades down the line.
Review Security Features
Evaluate Integration Capabilities
Consider Cloud-Based Solutions
Analyze Upgrade Paths
Finally, make sure any 3D configurator selected has an upgrade path available so that it can keep up with changing technologies over time. This ensures that new features are constantly being added which helps increase productivity while also ensuring compatibility with other systems used within your organization. It’s also important to review pricing structures associated with upgrades so there aren’t unexpected costs associated with keeping up with changing technologies over time.
Get Feedback From Employees
After narrowing down potential choices, get feedback from employees who will be using the software on a daily basis. Ask them questions about usability, feature preferences, and any issues they may have encountered while using similar products in order to get an idea of what would work best within their workflow. This will help ensure everyone involved feels comfortable using the software once it’s implemented which makes onboarding smoother while helping improve overall efficiency long term.
Implementing a 3D configurator in your factory - the do's and don'ts
The implementation of a 3D configurator in your factory can certainly bring significant advantages to your manufacturing process. Streamlining processes and increasing efficiency is crucial in today’s fast-paced business landscape. However, there are certain factors to consider when deciding on which software to integrate into your operations.
By following the below do’s and don’ts, the integration of a 3D configurator can be a seamless and effective initiative for your organization.
By adhering to these do’s and don’ts, your organization can make informed decisions, execute a successful integration, and fully leverage the benefits of a 3D configurator in your manufacturing processes.
Do’s |
Don't's |
---|---|
Thorough Research: Take the time to research various 3D configurator software options available in the market. Evaluate their features, compatibility with your existing systems, customer reviews, and support services. e | Rushed Decision-Making: Avoid making hasty decisions when selecting a 3D configurator. Take the time to evaluate options thoroughly and choose the one that best fits your manufacturing needs. |
Identify Specific Needs: Clearly define your manufacturing requirements and objectives. Look for a 3D configurator that aligns with your specific needs and can address your unique challenges. | Ignoring Compatibility: Ensure that the chosen 3D configurator integrates smoothly with your existing manufacturing systems and processes. Compatibility issues can lead to operational disruptions. |
Seek Vendor Support: Engage with reputable vendors who offer excellent customer support and assistance during the integration process. A responsive support team can help resolve issues and ensure a smooth implementation. | Neglecting User Feedback: Listen to feedback from your employees during the implementation phase. Address their concerns and suggestions to enhance user adoption and overall success. |
Plan and Test: Develop a detailed implementation plan, including testing procedures. Conduct comprehensive testing to identify any potential issues or compatibility problems before full-scale deployment. | Overlooking Data Security: Prioritize data security and choose a 3D configurator with robust data protection features. This is especially crucial when dealing with sensitive manufacturing information. |
Employee Training: Invest in proper training for your team members to effectively use the 3D configurator. Well-trained employees will maximize the benefits of the new system and prevent user errors. | Neglecting Training: Do not skip or skimp on employee training. Insufficient training can lead to confusion and errors, hampering the benefits of the new system. |
Start with Pilot Projects: Consider starting with smaller, pilot projects before a full-scale rollout. This allows you to assess the system's performance and address any early challenges with minimal impact on production. | Over-Engineering: Avoid overly complex configurations that might overwhelm your team or slow down the manufacturing process. Keep the system user-friendly and efficient. |
Regular Updates and Maintenance: Stay current with software updates and maintenance to ensure optimal performance and security. | Neglecting Maintenance: Once implemented, do not ignore regular software updates and maintenance. Regular maintenance ensures the system's longevity and optimal performance. |
By adhering to these do’s and don’ts, your organization can make informed decisions, execute a successful integration, and fully leverage the benefits of a 3D configurator in your manufacturing processes.
Testimonies from companies who improved their manufacturing process with a 3D configurator
Discover how the 3D web configurator is revolutionizing shed/cabin manufacturing. In this case study, the advantages of implementing a 3D web configurator for sheds/cabin manufacturing are thoroughly examined.
The cutting-edge technology is explored for its ability to facilitate faster design iterations, reduce costs, and enhance customer satisfaction through an intuitive and transparent customization process. Readers are invited to join in discovering how manufacturers are harnessing the potential of the 3D web configurator to revolutionize their business operations and elevate their customer offerings to new heights.
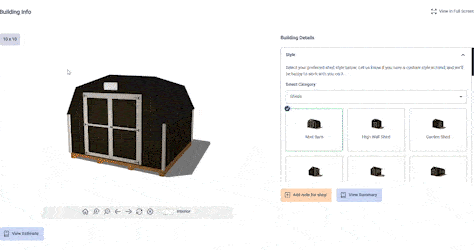
In a proprietary virtual application, Program-Ace elevates interior design to an unprecedented level of convenience.
Room Configurator is an HTML5 application that allows users to manipulate interiors with wooden, metal, or plastic elements. It offers a realistic virtual environment to explore and test materials, colors, and textures. Detailed plank information is available, simplifying product placement and enhancing sales potential. Users can project their major room assets with ease, getting a fast and effective product exploration across platforms.

With the right 3D Configurator, manufacturers can streamline their production processes and benefit from improved efficiency and accuracy. Manufacturers who are able to gain control of their manufacturing process by using a 3D Configurator can enjoy increased customer satisfaction, reduced overhead costs, quicker delivery times, better quality control, more flexibility in customization options, and overall productivity improvements.
Overall, 3D Configurators present an incredible opportunity for businesses to take a much needed step forward into the future of efficient and productive manufacturing. It is safe to say that by taking advantage of this powerful technology now, organizations may enjoy a considerable competitive edge over those still clinging on to outdated methods often requiring manual labor.
So what are you waiting for? Build your product smarter – get on board with 3D configurators!
If you’re ready to start utilizing advanced 3D configurator technologies for making your product visuals truly stand out from the rest, contact the emote3D team today via our contact page or call us directly at +91(944).278.9110.
Our experienced team of 3D configurator developers from India is here to help you get started on your journey toward enhanced visualizations!